Passive cold chain transportation methods broadly refer to any method of transportation of cold chain items that does not involve outside power or maintenance. Passive systems are self-contained and are prepared at the point of origin without continued management by the transporter, other than some basic duty of care.
Passive Cold Chain Containers
Some medical related relief items – such as vaccines and other lifesaving medications – rely heavily on passive cold chain containers for transport in humanitarian field settings. Passive cold chain containers are insulated carries, usually with accompanying ice packs and/or freeze packs, which require no external power or mechanical support and are especially useful in humanitarian contexts where persistent electrical connectivity or advanced infrastructure may not be available or actively working. Passive cold chain containers - either single use disposable or reusable depending on the context - and are only meant to keep cargo items in a pre-defined temperature range for a limited period of time, between 12 hours and 120 hours depending on the container and the external ambient temperature. Please note, the actual duration of passive container will depend on the container and the real-world conditions on the ground. For relatively short transit times, such as single day car rides, or movement via helicopters, passive cold chain containers are ideal for transporting small quantities of items.
There are two main type of devices - reusable containers (cold boxes and vaccine carriers) and disposable boxes. Note: the term “disposable” does not mean these types of insulated boxes can only be used one, they only refer to the easily disposable nature of the materials. Disposable insulated boxes are frequently reused multiple times in single operation.
Cold Boxes – Insulated reusable containers that loaded with coolant packs are used to transport supplies between different medical stores or to health facilities. They are also used to temporarily store items when the refrigerator is out of order or being defrosted.
The storage capacity of cold boxes ranges between 5 and 25 Litres and its cold life can vary from a minimum of 48 hours to a minimum of 96 hours (known respectively as “short range” and “long range” cold boxes).
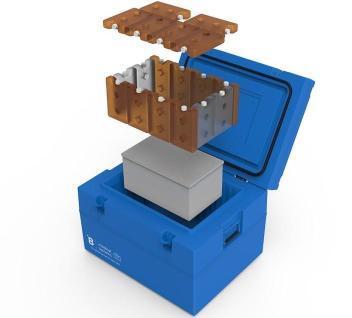
Vaccine Carriers - Insulated reusable containers that, when lined with coolant packs, keep vaccines (and diluents) cold during transportation from health facilities with refrigeration to vaccination sites where refrigeration and ice are not available. They are smaller than cold boxes and therefore easier to carry by a single health worker travelling on foot or by other means, where the combined journey time and immunisation activity ranges from a few hours to a whole day. The storage capacity of vaccine carriers is between 0.1 and 5.0 Litres.

Disposable Insulated Boxes - (also known as Insulated shipping containers) Insulated containers, manufactured in carton or moulded foams such as polyurethane, polyethylene or expanded polystyrene (EPS). Some are designed for single use while others are returnable for reuse. They are used for the transport of items over long distances. Their storage capacity, temperature range, cold life and resistance vary among different solutions: some solutions are suitable for Road transport with hold on times between 36-48 hours while some other solutions are suitable for air transport with hold on times up to 120 hours. One main concern related to disposable insulated carton boxes is its single-use lifespan and its low-cost material composition of EPS and water-based gel packs, rarely recyclable.
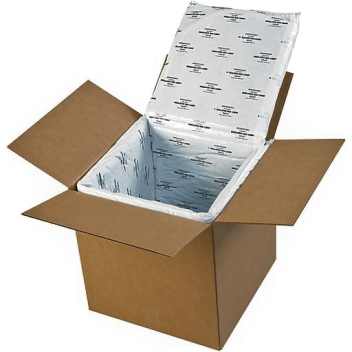
Disposable insulated carton boxes are used by manufacturers to ship products with sensitive cold chain needs around the world. Disposable insulated containers must conform to certain standards, and often have a cold life often with a maximum of 4 days. Insulated containers are regulated by WHO prequalification standards.
Three categories of packaging are used for international air freighting (listed below in decreasing order of bulk):
Class A | Packaging is designed to ensure that the temperature of the item does not rise above +8°C for a minimum exposure of 48 hours at an ambient temperature of 43°C. |
---|---|
Class B | Packaging is designed to ensure that the temperature of the items does not rise above +30°C for a minimum exposure of 48 hours at an ambient temperature of 43°C. It must also prevent the temperature of the items from dropping below +2°C for a minimum of 48 hours at an ambient temperature of -5°C. |
Class C | Packaging provides no specific protection against high temperatures. However, it must prevent the temperature of the item from dropping below +2°C for a minimum exposure of 48 hours at an ambient temperature of -5°C. |
No matter the type of passive insulated carrier used, it is recommended that each insulated carton should weigh less than 50kg to ensure ease of handling during transport as they are frequently loaded and offloaded manually.
Pallet Shippers
Pallet shippers are passive insulated packaging that is specifically designed to cover or encompass entire pallets of cold chain related items. Pallet shippers can come in the form foam insulation, cardboard, or some form of thermal resistant fabric. Pallet shippers are used mostly by commercial providers shipping bulk volumes of cold chain required medical products.
Example pallet shippers:
Pallet shippers have a built-in wooden or plastic pallet platform to enable handling and transport by forklift or pallet handling equipment. Pallet shippers will generally accommodate higher volumes per unit. Where used or ordered, It is recommended that external dimensions of pallet shippers should not exceed standard ISO pallet sizes, while also not exceeding not exceed 160 cm in height. Height requirements may vary on the context, but 160 cm is generally the maximum height a pallet can be to fit as a single unit into most aircraft. Shippers should understand the ultimate transport requirements prior to using pallet shippers. Under no circumstance should pallets shippers be depalletized in transport, or double stacked!
Transporting Passive Cold Chain Containers
Irrespective of the method, transportation of passive cold chain containers generally should follow a few key steps:
- Wherever possible, passive cold chain containers and boxes should be covered, and kept away from direct sunlight.
- Containers should be kept away from ambient heat sources of excessive heat (such as engines)
- Transportation times should be kept well within the allotted limit of the passive keep cool container. Ideally, maximum transport times should not exceed 2/3 the anticipated duration of the capacity for the container to keep items cool. In many cases, transport times should also be based on the anticipated return journey times, in case cargo items are rejected or may not be able to offload for a variety of reasons.
- Persons receiving the passive containers should be notified in advance and be waiting at the reception area.
- Depending on the nature of the operation, or the requirements for the cargo items, temperature monitoring devices may be included. For more information on monitoring devices, please reference the section on temperature monitoring in this guide.
Additionally, a general checklist for transporting passive cold chain containers might include:
Pre-shipment actions: |
|
---|---|
Shipping day – actions at point of origin: |
|
Actions during transit: |
|
Arrival day: actions at destination: |
|
Post-shipment actions: |
|
Adapted from: WHO - Temperature-controlled Transport Operations by Road and by Air
Planning Passive Keep Cool Container Transport
Use of Portable Passive Keep Cool Containers
Due to infrastructure and logistics constraints in some locations, it is advised to assess the logistics capacity of downstream reception facilities prior to shipping. In case of limited logistics capacity, it is preferable to ship keep cool items using individual insulated cartons.
Cold Boxes | Reusable containers generally used to transport keep cool items from one fixed store to another, and from central stores to health facilities. They have a storage capacity between 5.0 and 25.0 litres. There are two types of cold boxes:
|
---|---|
Vaccine Carriers | Used for transporting vaccines where the combined journey time and immunisation activity ranges from a few hours to a whole day. The vaccine storage capacity of vaccine carriers is between 0.1 and 5.0 litres. |
When choosing means for transport of keep cool items, consider the following factors:
- The heat and freeze sensitivity of every keep cool item being transported, especially vaccines. If available, refer to manufacturer indications for further information on temperature sensitivity of the items. In any other case refer to WHO How to use passive containers and coolant-packs.
- The required cold life to keep transported keep cool items at safe temperatures for an entire transport or outreach session. For vaccination outreach sessions the considered time should include travel to and from the vaccination site, allowing the safe management of non-used vaccines.
- The required capacity based on the volume of keep-cool items to be transported.
When selecting the appropriate container, the time of transport must be considerably less than the cold life of the container. Unexpected events such as vehicle breakdowns, human error or carelessness, often delay the time of transport. When the duration of the journey exceeds the cold life of the container, it is possible to replace the coolant packs if necessary. The back-up coolant packs can be transported in a separated container or swapped in a stop-by storage facility with compatible coolant packs. It is therefore necessary not to compromise on the number of ice packs which may need to be prepared.
Coolant Packs
Once the decision about the type of container is taken, calculate the number of cold boxes required. Subsequently calculate the number of coolant packs and temperature tracking and alert devices required. Each container holds a specific number of coolant packs.
In regular cold chain management, it is recommended that every cold box or vaccine carrier should have at least two sets of coolant packs, allowing one set of the packs to be cooled, while the other set is being used in the cold box or vaccine carrier. Note that one set of coolant packs is normally provided with each procured cold box or vaccine carrier, so that one additional set at least needs to be ordered.
The type of coolant packs must be selected according to the container and the required temperatures. Ideally, they should be compatible with other coolant packs used in the country.
There are several types of coolant packs:
Water-Filled Coolant Packs | The most commonly used, they are available in a solid rectangular plastic container in different sizes. The most common are: 0.3 litres (in two different sizes: 173x120x26mm and 163x90x34mm), 0.4 litres (163x94x34mm) and 0.6 litres (190x120x34mm). They are used to maintain temperatures in reusable cold boxes or vaccine carriers. WHO currently recommends the use of water-filled coolant packs. Drinking water is safe for such use and is generally available; this makes it the most practical substance for filling coolant packs because both water and ice can effectively control the temperature of the load, when correctly used. |
---|---|
Gel-Packs | sealed coolant containers pre-filled with a mixture of water and additives. They are available in flexible plastic bag or in a rectangular plastic container. WHO does not recommend using gel-packs because their thermal properties - freezing point of some gel-packs can be significantly below 0°C - and their lower durability. |
Phase-Change Material Packs (PCM-packs) | containers filled with other phase-change materials different from water. They can be designed to change phase at the convenient temperatures range, overcoming the risk associated with frozen water. However, they are also more expensive, and their conditioning process is longer and more complex. |
Depending on the urgency of the item, manufacturers of cold chain and keep cool items ship products by air using coolant-packs of various types and sizes containing various fill materials, including water, gel and PCM. It is a common practice to reuse these coolant packs recovered from international shipping containers. WHO discourages this practice as these packs do not necessarily perform in the same way as the water-packs. In addition, they are not designed for repeated use and may not be dimensionally compatible with most of the passive containers used for the in-country supply chain. The recommendation is that these packs are removed from the receiving keep cool items and recycled or disposed of according to the manufacturer’s recommendations and/or national waste management policies.
Conditioning Water-Packs
The temperature of coolant packs must be set according to the temperatures required by the keep cool items to be shipped. There are two main possibilities:
- The items to be shipped in the cold box may be frozen. Examples: vaccines for Measles, Polio, Yellow fever, Meningitis, etc.
- The items to be shipped in the cold box will be irreversibly damaged when frozen Examples: Oxytocin, vaccines for DTP, DT, Td, TT, Hep A and Hep B, Hib.
To understand if items can be safely frozen or not, consult the manufacturer’s guidelines. If all items to be shipped in the cold box may be frozen, frozen coolant packs can be directly transferred from the freezer to the cold box.
In the case that items will be damaged when frozen, the coolant packs need to be “conditioned” before being transferred into the cold box. That means bringing its temperature up to 0ºC. The conditioning of coolant packs consists of laying the required number of frozen icepacks on a table or work surface (preferably not under direct sun light) and waiting until they all reach 0ºC. This may take at least 30 to 45 minutes in hot weather and much longer in cool conditions (from 90 to 120 minutes at +20°C). In order to know when the icepacks are ready to be used, there must be liquid water inside every pack and the ice cores should be able to move freely inside the packs when shaken. To ease the process, place the icepacks in one single layer and separated from each other.
The use of cool water-packs and warm water-packs can be pertinent for some shipments. Warm water-packs are used to protect freeze-sensitive items in countries where temperatures are frequently below 0°C. Warm water-packs are to be prepared at a room temperature between +18°C and a maximum of +24°C. Cool water-packs are to be prepared in a refrigerator at a temperature of no more than +5°.
Packing Keep Cool Containers
The first action during packing is to dry any droplets on the coolant packs surface and placing it in a cold box according to the cold box manufacturer specifications: the correct size and number of coolant-packs must be used. The technical sheet for loading the cold box is often available inside each box.
Place the keep cool items inside the cold box, putting cardboard between thermo-sensitive products and icepacks to prevent them touching. Make sure that any remaining space is filled with packing material to avoid damage during onward transport.
When packing keep cool items without secondary package/carton box (common practice when using vaccine carriers), put the items and diluents in a plastic bag in the middle of the cold box or carrier to protect them from damage due to condensation.
Place the required temperature monitoring devices in the box or carrier. Do not allow monitoring devices to come into contact with coolant packs. If using a thermometer in the container, place it in a visible and easily accessible place to avoid long content handling during temperature checks.
When required, put the top layer of coolant packs and close the container.
Calculating Volumes for Vaccine Shipments using Keep Cool Boxes
To calculate the volume of vaccine to be shipped, it is necessary to know for each vaccine and diluent in the shipment:
- The required storage temperature: 3 ranges of temperature are normally considered for vaccine transportation: -15°C to -25°C, +2°C to +8°C or ambient.
- The number of doses to be transported.
- The packed volume per dose (cm3/dose). The packed volume includes the vaccine vial, the packet containing the vaccine vial and any intermediate packaging (secondary packaging).
The maximum recommended packed volume per vaccine dose and diluents are:
Vaccine type | Dose per vial | cm3 per dose |
---|---|---|
BCG (freeze-dried) | 20 | 1.2 |
DTP, DT, Td, TT | 10 | 3.0 |
20 | 2.0 | |
DTP-HepB | 2 | 6.0 |
10 | 3.0 | |
DTP-Hib | 10 | 2.5 |
DTP+Hib (freeze-dried) | 1 | 45.0 |
10 | 12.0 | |
DTP-HepB+Hib (freeze dried) | 1 | 22.0 |
2 | 11.0 | |
HepB | 1 | 18.0 |
1 in UNIJECT | 30.0 | |
2 | 13.0 | |
6 | 4.5 | |
10 | 4.0 | |
20 | 3.0 | |
Hib (liquid) | 1 | 15.0 |
10 | 2.5 | |
Hib (freeze-dried) | 1 | 13.0 |
2 | 6.0 | |
10 | 2.5 | |
Measles (freeze-dried) | 10 | 3.5 |
MMR (freeze-dried) | 1 | 16.0 |
10 | 3.0 | |
MR (freeze-dried) | 10 | 2.5 |
Meningitis A&C | 20 | 2.5 |
50 | 1.5 | |
OPV | 10 | 2.0 |
20 | 1.0 | |
TT in UNIJECT | 1 | 25.0 |
Yellow fever | 5 | 6.5 |
10 | 2.5 | |
20 | 1.0 | |
Diluent for BCG | 20 | 0.70 |
Diluent for Hib | 1 | 35.0 |
10 | 3.0 | |
Diluent for measles, MR, MMR | 1 | 20.0 |
10 | 4.0 | |
Diluent for meningitis A&C | 20 | 2.5 |
50 | 1.5 | |
Diluent for yellow fever | 5 | 7.0 |
10 | 6.0 | |
20 | 3.0 | |
OPV droppers | n/a | 17.0 (per unit) |
Diluent for BCG | 20 | 0.70 |
Be aware that the volume obtained from multiplying the packed volume per dose by the number of doses only takes into consideration the primary and the secondary packages: it doesn’t include the cold box packaging. Estimating the final transport volume (including the cold box) is necessary to correctly plan the transport means. For this purpose, a transport box bulking factor can be used. The bulking factor depends on the type of vaccine. WHO Guideline for establishing or improving primary and intermediate vaccine stores, recommends the following transport box bulking factors:
- BCF, OPV, measles, MMR, MR = 6.0
- Other vaccines = 3.0
- Diluent, droppers = 1.5
Type of Vaccine – The type of vaccine is of key importance because different vaccines have different presentations. The most common are vials (or ampules), however single-dose pre-filled syringes may be used in humanitarian operations. Depending on the vaccine, vials can contain different number of doses, normally 1, 10 or 20 doses. The key variables used to calculate the required volume for vaccine storage and transport are the number of doses to be stored and the estimated volume per dose. The estimated volume per dose (or packed vaccine volume) quantifies the space needed to store or transport vaccines and diluents and will depend on the number of doses per vial, the physical size of the vial or ampule (primary package) and the bulkiness of the external packaging (secondary packages).
Example multi-dose vaccine vial:
Example single-dose pre-filled vaccine syringe:
Some presentations include the diluent in the same packaging as the vaccine. In such cases it is necessary to refrigerate the diluent as well as the vaccine. In all cases, diluents should be refrigerated 24h prior to vaccine preparation. Refrigeration of diluents is normally done in the last step of the vaccine supply chain.
Whenever possible, the packed vaccine volume per dose should be calculated using data from the vaccine manufacturer or supplier. It is also recommended to use the WHO guidance document for vaccine volume calculation: How to calculate vaccine volumes and cold chain capacity requirements.