General Storage Guidelines for Medical Items
In any storage location where health items might be stored, there are several general rules that will help avoid loss to stock through damage or unanticipated expiration date.
Item Placement and Visibility:
- Avoid storing boxes, or exposed health items in places that receive direct sunlight. Even short periods of exposure to sunlight can damage some health items, especially those labelled as light sensitive.
- Unless there is an advanced inventory management system in place, stock cards are strongly recommended. Stock cards should contain information on:
- Batch numbers.
- Expiration dates.
- Temperature ranges.
- Product codes.
- Programmatic use.
- Avoid mixing the same medication from different batches/expiry dates – if your storage facility is warehousing the same health item but from different batches/expiry dates, those items should be kept separately, and recorded separately.
If storing health items in cartons:
- Ensure that cartons with arrows indicating which side should be facing upward are properly followed.
- Ensure cartons are properly labelled, with contents, expiration dates, batch, and other relevant information visible. If no labels are used, or the boxes come unmarked, write the relevant information on the side.
- Follow manufacturer’s directions on stacking and handling.
It is always important to remember that the majority of health items are classified as fragile. Handling personnel and practices should be in place to ensure safe management of goods.
Any storage facility used to store health commodities protect all items from physical damage, moisture, excessive heat or cold, sunlight, dust, dirt, and pests. Cleanliness in a warehouse used to store medical items is of even more importance than it is for some other categories of commodities.
Colocation with Other Materials – Pharmaceuticals and medical support devices should always be stored separately from chemicals or food. Examples of chemicals commonly found in humanitarian contexts might include:
- Pesticides
- Fertilizers
- Cleaning agents
- Fuel
- Foodstuffs and bulk food items
However, even non typically hazardous materials – such as bags of cement – can impact health items, both in storage and in transport. Wherever possible, health related items should be stored in adequately prepared and separated spaces.
Shelving:
The use of shelving is very common when managing health items. Shelving is useful for easily storing small quantities of a large number of SKUs, enabling storekeepers to withdraw discrete quantities of items while still being able to neatly segregate and track them.
Frequently shelving is used in the same location as racking; racking is better suited for managing large cartons or pallets and may be used before the cartons are open and the line items are broken down into discrete inventory units, while shelving is better suited for managing individual units that are withdrawn on a case by case basis. Both have their use cases in health facilities.
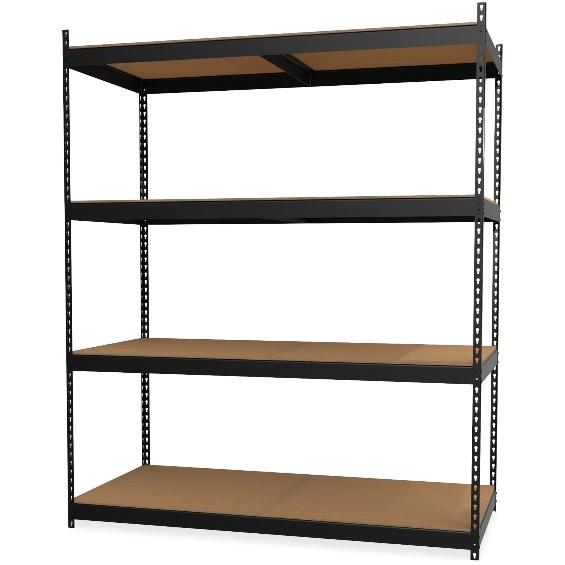
In addition to the normal practices of using shelves, there are some special considerations when using shelves to store health items:
- Place glass vials on the bottom shelf to minimise risks of damage from falling items.
- Place liquids on the bottom shelf to avoid damaging other items in case of a rupture or leakage.
- Ensure that all items are clearly visible, and when labelled, labels are legible.
- Even if the quantities are small, use stock cards to record transactions. Multiple stock cards can be kept in a single pouch or container to save space.
- In storage areas with temperature zones, temperature sensitive health items should be stored where temperatures are most appropriate for their manufacturer specified requirements, usually on the lower shelves.
Palletisation:
If health items are stored in pallets, there are some key rules for proper management beyond the regular guidelines for managing pallets and ground stacking:
- All cartons containing health items should be clearly labelled with relevant information, and labels should be outward facing and visible.
- Medications are frequently light, and sub-packaging may have much empty space – cartons containing health items might be easily crushed or damaged and should not be stacked to excessive heights. Never exceed 2.5 meters as a maximum height of cartons stacked on a pallet, and ideally less height where possible.
- When storing pallets with multiple types of health items, pallets may need to be physically separated by a minimum of 30 centimetres to allow access to all sides of the pallet for inspection and handling purposes.
- Where possible, store like-items together, such as health items from the same batch and with the same expiration date. Intermixing different items will make picking specific items more difficult.
- The use of heat treated, or plastic pallets is recommended for storing health items wherever possible.
Damaged and Expired Health Items
Due to the sensitive nature of pharmaceuticals and other medical devices, it is extremely important that managers of health stores monitor, identify and isolate damaged or expired items for proper repair or disposal and prevent accidental release of such items into distribution to avoid harm to end user.
Managers of health items should always track the expiration dates of health items, and routinely conduct inspections and physical inventory counts to ensure any and all instances of expiration or damage are captured. The intervals required for inventory counts of health items may be more frequent that non-medical items, and managers may wish to conduct a physical inventory every three months or even once a month. Based on the number of individual line items in any medical store, a full physical inventory may be prohibitively complex, so managers may also wish to conduct random sampling on an ongoing basis, with intermittent physical inventories through the year.
Health items that have been identified as either damaged or expired should be removed from their regular location in the storage space, and isolated in a specially identified “quarantine area” within the storage facility. A quarantine area doesn’t mean that health items are infectious, but rather they are to be treated separately from the rest of the items on stock. Quarantine areas should be:
- Clearly marked and labelled as being stock that cannot be issued as regular stock.
- Clearly physically separated from main stock items. This might include painted areas on the floor, or possibly even separate rooms.
- Ideally, quarantine areas should be lockable, and keys should be kept with the warehouse manager.
- In some contexts, the isolation and management of damaged/expired health items might have specific regulations, including secure monitoring and time limitations. Logistics personnel should consider local laws prior to designing a quarantine strategy.
Items placed in quarantine should:
- Be tracked separately from non-impacted stock items, including their own stock cards and their own record in an electronic inventory system.
- Be prepped and ready for disposal.
- Any medication, be it expired or damaged should not be considered fit for human consumption and should be disposed of safely and in a manner in compliance with local regulations. Please reference the section on medical waste management for more information.