Drums
The global standard for storing and transporting fuel in drums is the 200 litre metal drum. There are however multiple variations, including metal drums and containers of various sizes, and drums made from plastic. Drums are useful because they are mobile, and can be moved and stored as single units, however basic caution must be taken.
Drums should be stored on pallets, separated from the ground. Though ground storage is possible, pooling water from rain/flooding, or other spilled chemicals can impact containers and contents. Pallets used for drum storage should be sturdy and not structurally compromised. Drums stored on pallets should be centred on pallets and not hanging off edges.
Drums used for storage should be in safe, usable condition. A drum in good condition:
- Should not leak.
- Should not display excessive signs of rust.
- Should be able to be safely and tightly sealed/resealed.
- Should not be so bent/damaged that it cannot be safely moved or stored.
- Should not have debris or dirt inside.
Fuel contained in a leaking drum should be transferred without delay to a drum in good condition. Be aware that there is no effective way to seal a leaking drum that is full. Drums can be sealed by welding, which should never occur around any amount of fuel. Leaks are often caused by improper handling of drums.
Full/partially full drums should not be double stacked unless there is a proper and safe racking system in place. Avoid placing full drums on top of other full drums. NEVER stack above two drums high. Full/partially full drums should be stored sitting upright. Drums should only be stored on their sides if:
- There is a safe and purpose built structure that can support the weight of the drum and contents.
- The drums are completely resealable and will not leak.
- The drums are empty.
Storing fuel in drums can be considered “modular” because the numbers and types of drums can change based on need while a fuel tank is static. There are however challenges when managing fuel in drums.
Drums containing different types of fuel should be completely segregated, ideally with a physical structure or sign differentiating the different types. Drums should be clearly marked as containing fuel, or not mislabelled as mislabelled as containing something else. Labels should clearly indicate the type of fuel contained inside, and the date of purchase. Intermixing of fuel types can cause problems – the wrong fuel placed in the wrong engine can permanently disable vehicles and generators.
The general rule is that fuel should be dispensed under the First In/First Out (FIFO) rule – the oldest fuel should be consumed first, and stock cards and warehouse ledgers should clearly reflect purchase dates. Long term storage of fuel should be in metal drums or containers.
For handling and moving drums comes with its own safety needs. Wherever possible persons moving drums should wear gloves.
Ideally, drums should be moved using safely operated handling equipment:
- Right sized hand truck or dolly to move individual drums.
- Drums can be moved on a pallet using a forklift, however drums must be braced and secured on the pallet.
Drums can be rolled to vehicles/storage locations, however:
- The ground must be smooth, and free from hazards that can puncture a drum or generate sparks.
- Drums must be tightly sealed.
- Ramps or planks can be used to move up and down between two hights, but inclines should not be more than 30 degrees.
Care must be taken when opening and working around open drums. Fuel drums that are hot to the touch should be opened very slowly to avoid rapid release of pressurized content. When opening drums, the tops of drums should be cleaned off to avoid debris falling into the fuel. When checking fuel levels, use a “no-spark” dipstick – any clean wooden stick or ruler can be used to identify height within drums.
Tanks/Reservoirs
Fuel tanks are widely considered the best practice for large scale or long term (up to six months) storage of fuel.
Tank/reservoir storage has many advantages:
- Capable of storing and moving high volumes of fuel relatively efficiently.
- Allows for adequate and necessary electronic and remote monitoring equipment.
- Minimizes accidental spills.
There are multiple configurations for tank storage, the advantage of which is scale ability. General rules for managing fuel tanks:
- The total volume stored in tanks should not exceed anticipated six months’ worth of consumption.
- Tanks should be in well ventilated, and well shaded.
- Tanks should ideally have built up walled structures around them. Walled structures will need to have the appropriate holes to run fuel lines in and out of the secured space.
- If tanks are stored in the open, there should be a protective crash barrier surrounding them.
- If tanks are stored in recessed or below ground, dug-out spaces, the site should not be prone to flooding, and here should be adequate drainage.
- Tanks should be in good condition, without leaks or signs of distress.
- If different types of fuel are stored in different tanks, they should be clearly marked and clearly separated, possibly by a physical barrier.
- Tanks generally require cleaning every six months, both inside and out. When tanks are cleaned, all lose debris, build up and any other substance should cleaned as much as possible.
- Inspections around a fuel tank should be conducted several times a year to look for signs of degradation, warping on leaking.
- Some tanks are installed with a slight incline to enable evacuation from a dedicated drain.
- In some contexts, permanent fuel storage will require special signage under local regulations. Consult with local authorities on regulations regarding marking fuel tanks.
- Using multiple tanks can function like a FIFO system – with fuel only being refiled one tank at a time, enabling distributors to “cycle” through oldest fuel first.
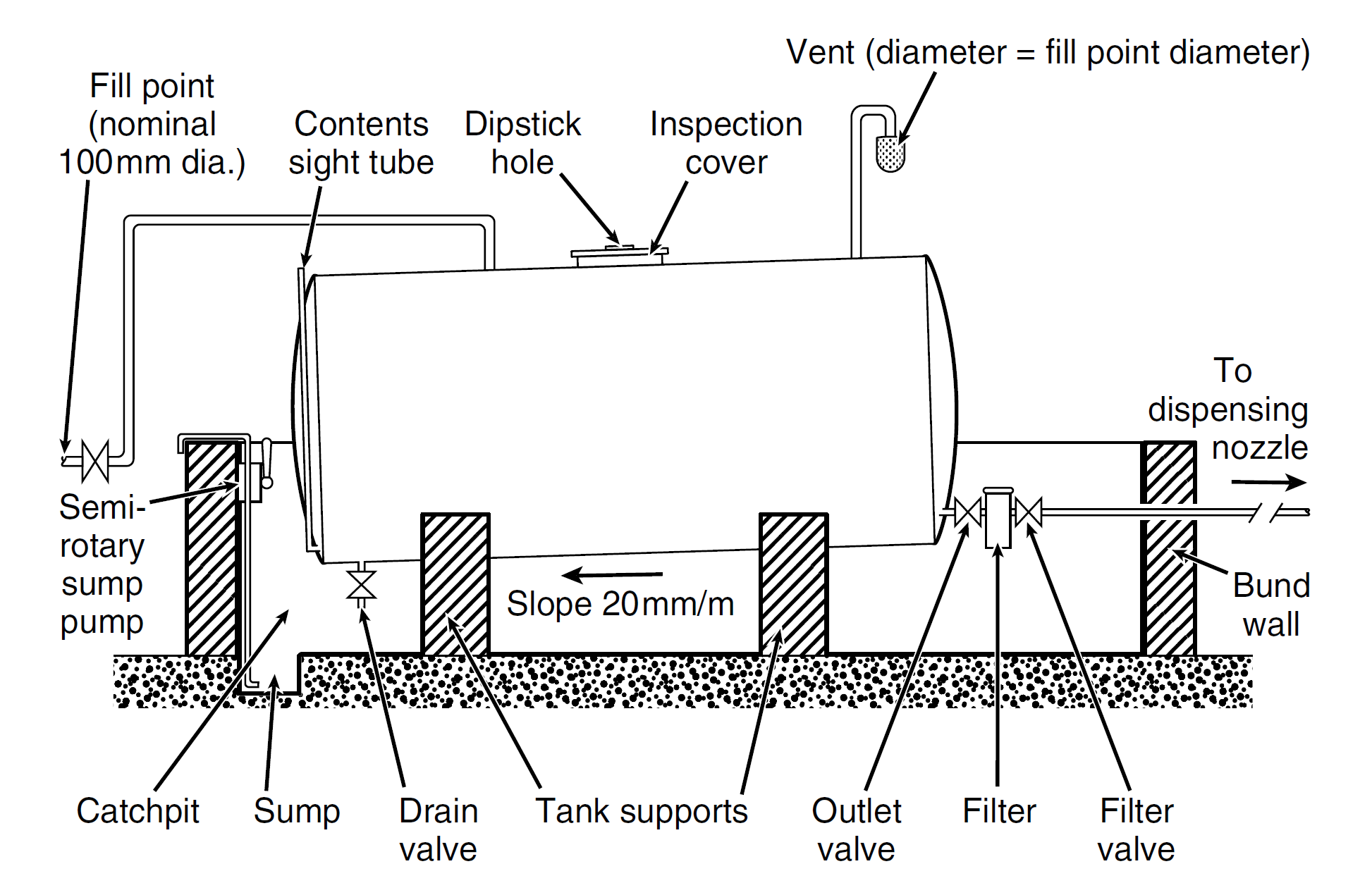
Source: Red R, Engineering in Emergencies
In general, tanks will come with a variety of openings, perforations.
Fill/Discharge – Tanks should have at least one valve dedicated to refilling and/or discharging fuel for regular consumption. Sometimes tanks will have multiple lines, one for refilling and one for discharge. Discharge lines should never be at the very bottom of the tank, and should be at least 1/10 of the height from the bottom.
Drainage – Used for draining tanks completely so cleaning/debris removal can be undertaken.
Air Intake – A small inlet to equalize pressure when discharging fuel, or to release pressure build-up when temperature differences between the outside and inside of the tan.
Inspection Cover – Depending on the tank, there may be one or more larger openings that allow for dipsticks, visual inspection, cleaning, or other activities. Sometimes inspection covers are used for refilling as well.
Connected Fuel Tank Systems
Tanks can be networked or linked where required.
Linked tanks enable storage planners to “right size” their storage needs, using as much or as little storage as required. Linked tanks can even be used to push fuel between reserves with specialized equipment and pumps.
Installation and use of networked fuel tanks generally requires fairly advanced knowledge. Agencies thinking of installing and managing larger fuel reserves should first solicit outside companies that have experience with these types of projects.
Fuel Bladders
In some contexts, agencies may employ flexible fuel bladders to store fuel. Fuel bladders have the advantage of being collapsible, meaning they are easier to transport and warehouse. This makes them extremely useful for prepositioning and rapid deployment.
Before using bladders for fuel storage there are some points humanitarian agencies should consider.
Though fuel bladders can be used for long term storage, agencies should always consider permanent hard-sided structures where available. In the event a bladder is deployed in an emergency, agencies should consider replacing them after a few months.
Fuel bladders should be made from PVC, or other chemical resistant material, and must be specifically made for the storage of fuel. Bladders should be UV resistant.
Bladders should be inspected for damage or tears along the seams before deployment/set up. Always follow manufacture recommendations for storage, handling, and overall life span. Bladder stored in excessive heat my experience degradation faster than normal.
Fuel bladders should follow the same precautions as other forms of storage. Bladders should:
- Be properly shaded.
- Clearly marked as containing fuel.
- Segregated by fuel types.
- Kept in a secured location with controlled access.
- Be kept away from open flames and sparks, and have adequate fire safety precautions taken at all times.